9. Mai 2022
Vorbild Antike: Bauen mit Zement soll klimafreundlicher werden
Bei der Herstellung von Zement fallen große Mengen CO2 an. Neue Mixturen und Treibhausgasrecycling sollen den Baustoff Richtung Kreislaufwirtschaft führen
Von der antiken Kuppel des römischen Pantheon bis hin zu den Megabauten der Moderne: Die Baubranche kam und kommt kaum ohne Zement aus. So imposant die Gebäude sind, die mit dem Baustoff errichtet werden, so zweifelhaft ist sein Ruf.
Die Zementindustrie steht aufgrund ihrer Treibhausgasemissionen immer wieder im Kreuzfeuer der Kritik. Zwar wird Zement in keinem Land der Welt ähnlich effizient hergestellt wie in Österreich, trotzdem entstammen hierzulande etwa drei Prozent der Treibhausgasproduktion der Zementindustrie. Weltweit liegt dieser Wert bei etwa 4,5 Prozent.
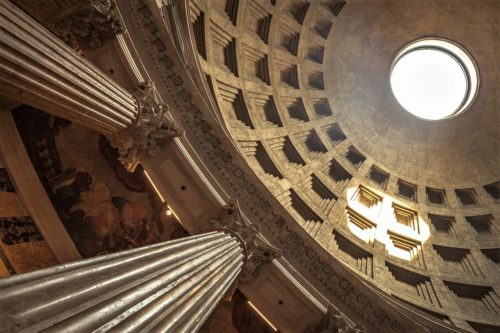
Das römische Pantheon, ein Wunderwerk der antiken Architektur – und mit dem „Opus caementicium“ hatten Roms Ingenieure auch das Wundermittel, mit dem sie solch gigantische und äußerst haltbare Kuppeln schufen. © pixabay
Sebastian Spaun, Geschäftsführer der Vereinigung österreichischer Zementindustrie (VÖZ), versucht deshalb die entscheidende Frage „Was kommt auf uns zu, und wie kommen wir in Richtung CO2-Neutralität?“ zu beantworten. Als Teil des Forschungsnetzwerks Austrian Cooperative Research (ACR) sucht die VÖZ gemeinsam mit dem Projektpartner Smart Minerals GmbH nach Wegen, Zement klimafitter und umweltfreundlicher zu gestalten. Der Hauptrohstoff von Zement ist der Kalkstein. Dieser wird gemeinsam mit Ton erhitzt und in weiterer Folge bei 1450 Grad Celsius zu Zementklinker gebrannt.
Klimafreundlich & stabil
Erst die dabei entstehenden Klinkerminerale verleihen dem Beton letztlich seine Festigkeit. Bei ebendiesem „Entsäuern“ entlässt der Kalkstein jenes CO2, das etwa zwei Drittel des gesamten CO2-Ausstoßes in der Verarbeitung des Materials ausmacht. Derzeit besteht Zement zu knapp 70 Prozent aus Klinker, und dieser macht den größten Teil der CO2-Bilanz aus. Laut Berechnungen ist eine Reduktion des Klinkeranteils auf 52 Prozent möglich. In der Produktion wird der Klinker in Zementmühlen mit anderen Stoffen zu Zement vermahlen.
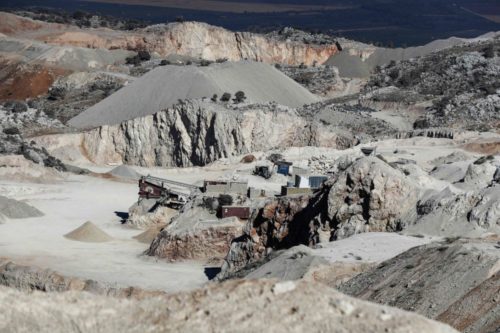
Die Herstellung von Zement gehört zu den klimaschädlichsten Prozessen bei der Betonproduktion. Rund drei Prozent der Treibhausgasemissionen in Österreich gehen auf das Konto der Zementindustrie. In mehreren Abschnitten der Produktion sucht diese nach Wegen, klimafreundlicher zu produzieren. © apa
„Bei einer weiteren Reduktion werden die Herausforderungen schon sehr groß“, sagt Spaun. Der Rest sind Zumahlstoffe wie Hüttensande aus den Hochöfen der Eisen- und Stahlproduktion sowie Flugasche, ein Abfallprodukt von Kohlekraftwerken. Doch die Tage der klassischen Zumahlstoffe sind gezählt, hat doch das letzte Kohlekraftwerk Österreichs in Mellach im Frühjahr 2020 seinen Betrieb eingestellt.
Hüttensand ist ein Überbleibsel beim Abtrennen des Eisens vom Erz. Die Voestalpine liefert zwar seit vielen Jahrzehnten den benötigten Hüttensand, doch auch die Stahlindustrie steht vor weitreichenden Änderungen zum Beispiel durch die Umstellung auf Elektroöfen. Somit wird sich der Hüttensand in Menge und Zusammensetzung ändern – inwieweit, ist noch ungewiss.
Neuer Zement aus altem Bauschutt
Eine Reduktion des Klinkeranteils wird etwa auch durch den Zusatz von feinem Betonabbruch erprobt, und mit Ziegelsplitt wird Ton im Rohmaterial substituiert. „Wenn man es so ausdrücken will, machen wir aus Bauschutt neuen Zement“, sagt Spaun. Natürliche Ressourcen zu schonen und Kreisläufe zu schließen sei schon seit Jahren ein zentrales Thema.
Dieser Weg wurde in Hinblick auf Alternativbrennstoff bereits vor 30 Jahren eingeschlagen. Das rentiert sich besonders dann, wenn sich globale Lieferketten verteuern oder ausfallen. Auch in der aktuellen Gaskrise wird noch einmal deutlich, wie wichtig die Unabhängigkeit der österreichischen Zementindustrie ist.
Die Emissionen der Prozessreaktionen des Klinkers können letztlich aber nur durch Abtrennung mittels Aminwäschern, Oxyfuel oder Membrantechnologien reduziert werden. Diese Technologien stehen auf unterschiedlichen Ebenen der Entwicklung. Da die Zeit auch in Anbetracht des voranschreitenden Klimawandels drängt, sollte man so bald wie möglich mit dem Bau von Pilotanlagen beginnen, denn das Hochskalieren braucht Zeit. „Wir werden bestimmt noch klüger werden auf dem Weg“, sagt Spaun.
CO2-Recycling im Fokus
Ein weiteres Problem stellt das abgeschiedene CO2 dar. Dafür arbeitet der Zementmarktführer Lafarge gemeinsam mit der OMV sowie dem Kunststoffhersteller Borealis und dem Verbund-Konzern an Lösungen, um aus CO2 und Wasserstoff mittels Synthese die Kunststoffe der Zukunft herzustellen. Dieses Konzept nennt sich Carbon to Product, wobei Kunststoffe nicht mehr aus Erdöl, sondern aus CO2 hergestellt werden. Das Carbon-to-Product-Verfahren wurde bereits beim Europäischen Innovationsfonds eingereicht.
Im Lauf der 170-jährigen Industriegeschichte sei noch nie so stark sektorübergreifend zusammengearbeitet worden wie heute, sagt Spaun. „Es ist an der Zeit, dass sich die Industrie neu erfindet.“ Unterstützt wird dieses ambitionierte Unterfangen auch von der Forschungsförderungsgesellschaft (FFG), die vom Klimaschutzministerium und vom Wirtschaftsministerium getragen wird. Eine der zu bewältigenden Herausforderungen ist es, bei der Dekarbonisierung die Leistung im Auge zu behalten, die in der Bauindustrie notwendig ist.
Die Idee ist, durch eine feinere Mahlung sowie eine bessere Abstimmung der Komponenten den reduzierten Klinkeranteil auszugleichen. „Zusätzlich müssen wir von einer linearen hin zu einer CO2-Kreislaufwirtschaft kommen“, sagt Spaun. Denn das Treibhausgas soll nicht mehr in die Atmosphäre entlassen werden. Zu diesem Zweck werden neue Kohlenwasserstoffe aus CO2 und aus erneuerbar erzeugtem Wasserstoff produziert. Alle Kohlenwasserstoffe, aus denen chemische Produkte und Kunststoffe produziert werden, können dann am Ende ihres Lebens wieder ins Zementwerk zurückgenommen werden. Es wird erneut Energie daraus gewonnen, die zum Brennen des Klinkers gebraucht wird, CO2 wird abgeschieden – und voilà: Es tritt wieder als neuer Grundstoff in den Kreislauf ein.
Die Hitze des Vesuv nachbilden
Bei der Beigabe der Zumahlstoffe kommt es auf die richtige Mahltechnologie und Mischung an, um für den klimafitten Zement das Beste aus allen Komponenten herauszuholen. Was nun dringend in den Mittelpunkt der Forschung rücken muss, sind neue Zumahlstoffe, da die herkömmlichen von der Voestalpine weniger werden und Flugasche importiert werden müsste. „Was der Vesuv für die Baumeister Roms war, das ist der Hochofen für die Zementindustrie“, erklärt Spaun. Es werden unter anderem Zumahlstoffe benötigt, die schon einmal „einen Vulkan erlebten“. Um hydraulisch zu sein, muss ein Stoff bereits einmal hohe Hitze erfahren haben.
Darum wird nun auf Ton gesetzt, welcher zuvor kalziniert werden muss. Ein Vorteil gegenüber dem Kalkstein ist, dass Ton beim Verbrennungsprozess kein CO2 freisetzt. Die ersten Erkenntnisse des Labors der Smartminerals GmbH, das die Eigenschaften des kalzinierten Tones untersucht, sehen durchwegs positiv aus. „Da kommt ein neuer Stoff daher, den die Römer schon hatten“, sagt Spaun.
Karin Grabner / DER STANDARD