Kategorie Innovation & Technologie - 28. März 2018
Der Heilige Gral der Materialwissenschaften
Erst weich und gut verformbar, dann möglichst hart, um etwa als Autokarosserie Sicherheit zu bieten: Aluminium wird in der Technik eine große Zukunft vorhergesagt. Zum Beispiel im Automobilbau, wo es darum geht, durch möglichst geringes Gewicht Treibstoff zu sparen, den Ausstoß von Schadstoffen zu minimieren und – vor allem bei Elektroautos relevant – die Reichweite zu erhöhen. So hat sich der Aluminiumanteil in Autos zuletzt binnen eines Jahrzehntes glatt verdoppelt. Die Alu-Legierungen der Zukunft sollen wahre Alleskönner sein.
„Der größte Vorteil gegenüber dem ,Hauptkonkurrenten‘ Stahl ist mit Sicherheit die geringe Dichte. Sie entspricht nur etwa einem Drittel von Stahl und macht Aluminiumlegierungen daher besonders attraktiv für Anwendungen, bei denen Massen bewegt werden müssen“, erläutert Florian Grabner, Forscher am Leichtmetallkompetenzzentrum Ranshofen (LKR), einem Teil des AIT Austrian Institute of Technology.
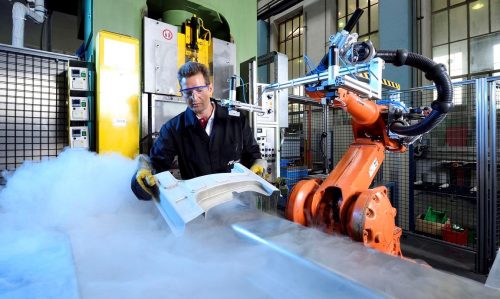
Mit flüssigem Stickstoff gekühlt, lassen sich aus Aluminiumblech auch sehr kompliziert geformte Bauteile herstellen. © AIT / Johannes Zinner
„Die Be- und Verarbeitung ist grundsätzlich nicht schwieriger als die von Stahl. Durch die grundlegend andere Mikrostruktur sind jedoch die mechanischen Kennwerte, z. B. die Festigkeit oder maximal mögliche Dehnung, von Aluminiumlegierungen zumeist niedriger als jene von Stahl. Diese mechanischen Kennwerte sind aber ausschlaggebend beim Herstellen von Blechbauteilen“, so Grabner, der am LKR das Projekt „KryoAlu“ leitet. Darin wird gemeinsam mit Partnern aus Wissenschaft und Industrie ein neues Verfahren zur Verformung von Aluminiumblechen entwickelt, das bisherige Schwierigkeiten umgeht.
Stand der Technik ist es, Aluminium bei erhöhten Temperaturen zu verformen. „Bei hohen Temperaturen ist der Werkstoff weich, das heißt, bei der Umformung sind hohe Dehnungen möglich. Jedoch ist die übertragbare Kraft geringer, was lokal zu Rissen im umgeformten Bauteil führt“, erklärt Grabner. Beim Erhitzen wird die Mikrostruktur verändert, sodass zusätzliche Prozesse notwendig sind, um wieder den Ausgangszustand zu erreichen.
Pressen bei minus 150 Grad
Die neue Idee basiert auf einer interessanten Eigenschaft von Aluminium: Auch bei tiefen Temperaturen verbessert sich nämlich die Umformbarkeit des Metalls – und dabei verändert sich die Mikrostruktur nicht. Im „KryoAlu“-Projekt – „kryo“ ist griechisch und bedeutet „kalt“ – wurde nun in den vergangenen Jahren ein Verfahren entwickelt, bei dem Bleche in flüssigem Stickstoff vorgekühlt, von einem Roboter in die auf bis zu minus 150 Grad gekühlte Umformpresse eingelegt und nach dem Tiefziehen wieder entnommen werden. Mit diesem innovativen Verfahren können künftig wesentlich komplizierter geformte Teile aus einem Blechstück hergestellt werden – so können z. B. mehrere Einzelteile einer Autotür zusammengefasst und aus einem Teil gefertigt werden; dadurch werden Fügestellen eingespart, zudem ist eine hohe Festigkeit und Oberflächengüte erzielbar. Diese Vorteile können je nach konkretem Einsatzgebiet die erhöhten Kosten durch die Kühlung wettmachen.
Allerdings: Von einem Prozess, der im Labor- und Technikum-Maßstab funktioniert, bis zu einem großindustriell anwendbaren Verfahren ist es noch ein langer Weg – der zur Zeit im Nachfolgeprojekt „KryoAlu2“ gegangen wird. Dabei geht es zum einen um die Entwicklung von für den Kryo-Prozess optimierten Aluminiumlegierung und zum anderen um die Lösung vieler technischer Details, wie etwa die Werkzeugkühlung oder die Schmierung. Die Forscher sind optimistisch, am Ende des Projekts einen vorserientauglichen Prozess präsentieren zu können, der auch auf die Großserie ummünzbar ist.
Neues CD-Labor in Leoben
Wie kann sich ein Material im Produktionsprozess gut verformen lassen und letztlich doch ein sehr festes Produkt bilden? Der Metallurg Stefan Pogatscher bezeichnet diese Frage als den „Heiligen Gral der Materialwissenschaften“. Einer Antwort will er als Leiter des am Mittwoch an der Montan-Uni Leoben eröffneten Christian-Doppler-Labors (CD-Labors) für Fortgeschrittene Aluminiumlegierungen zumindest ein Stück näher kommen. Die Ziele sind ehrgeizig: Man wolle neue Standards bei Aluminiumlegierungen setzen, sagt Pogatscher. Aus diesen sollen sich komplexere Bauteile für die Automobilbranche fertigen lassen, als das heute möglich ist; sie soll der Hauptnutznießer der neuen Entwicklungen sein.
- Herstellung einer neuen Aluminiumlegierung im Labor. © Kolb / Montanuniversität Leoben
- Stefan Pogatscher, CD-Labor für Fortgeschrittene Aluminiumlegierungen. © Freisinger
- Optimale Anordnung einzelner Atome zu Verbesserung der Eigenschaften. © Pogatscher / Montanuniversität Leoben
- Umgeformtes Bauteil aus einer industriellen Aluminiumlegierung. © AMAG
Bisher wird Aluminium in erster Linie in der Luftfahrt und für hochpreisige Autos eingesetzt. Dabei ließen sich bei Autos bis zu 40 Prozent des Gewichts – und damit auch CO2-Emissionen – einsparen, sagt Pogatscher. Neue Regulative zwingen Hersteller und Zulieferindustrie, ihre Produkte in dieser Hinsicht weiterzuentwickeln. „Mit der üblichen Bauweise aus Stahl geht das nicht“, sagt der Forscher. Und bisher genutzte Alu-Legierungen seien den hohen Anforderungen noch nicht gewachsen: Schließlich müssen sie einem Crash standhalten, sich aber auch zu gelungenem Design formen lassen. „Die Autos sollen ja nicht nur umweltfreundlich sein, sie sollen sich auch verkaufen.“
Neue Rezepte für Legierungen
Damit das gelingt, verfolgen die Wissenschaftler am CD-Labor zwei Strategien. Sie wollen erstens herausfinden, wie sich der Herstellungsprozess besser regeln lässt. Derzeit wird Aluminium nach dem Erwärmen abgeschreckt und härtet mehrere Stunden oder Tage lang unkontrolliert aus. Die Forscher experimentieren daher an neuen, besseren Rezepten für Alu-Legierungen. Durch beigefügte Spurenelemente wie etwa Zinn lässt sich die Härtungsreaktion präzise aus- oder einschalten. Zweitens versuchen sie, unterschiedliche Legierungsklassen zu kombinieren und so die jeweils besten Eigenschaften zu verbinden.
Das Team um Pogatscher am Lehrstuhl für Nichteisenmetallurgie baut in seinen Untersuchungen auf jahrelange Vorarbeiten auf, für die es 2016 bereits mit dem Houska-Preis, der am höchsten dotierten Auszeichnung für anwendungsorientierte Forschung in Österreich, belohnt wurde. Die Wissenschaftler simulieren die Vorgänge zuerst am PC, dann testen sie die Materialien im Labor, und schließlich untersuchen sie mit leistungsstarken Mikroskopen, was sich tief im Inneren verändert. „Wir wollen genau verstehen, was wir bewirken. Dazu müssen wir weit ins Material hineinschauen“, erklärt Pogatscher. Dazu wird in Leoben nun auch ein Rastertransmissionselektronenmikroskop angeschafft. „Die Atome von Zusatzstoffen gruppieren sich in Legierungen, das macht sie fester. Wir beobachten, wie schnell sie während des Aushärtens wandern und wohin“, so Pogatscher.
Anschließend testen die Forscher die mechanischen Eigenschaften und wie gut sich das Material verformen lässt – um dann am PC weitere Verbesserungen zu simulieren: ein Kreislauf, an dessen Ende in sieben Jahren – das ist die maximale Laufzeit eines CD-Labors – Aluminiumlegierungen stehen sollen, die den hohen, auch vom Industriepartner AMAG Rolling in sie gesetzten Erwartungen standhalten.